This is a sculpture project that the student Nico designed in his senior year as something to leave behind at Hawken’s upper school campus. The goal was to match the style of the surrounding buildings while also symbolically capturing the heart of Hawken. Nico wanted the sculpture to blend in with the architecture of the school rather than stick out and grab attention to itself. Yet he also wanted it to evoke the spirit of Hawken if someone were to look at it on its own. To satisfy both of these criteria the initial design idea was very simple: minimalist bird. The color scheme had to be very simple as well: white and gray (to match the architecture). And the sculpture had to be a bird to allude to Hawken’s mascot of the hawk.
To make this vision come true, Nico first started in Blender, where he used the sculpt tool to create a rough mesh of the sculpture he wanted to construct. From there, he sent the design to Fusion 360, and converted it into a solid body that he could later manipulate.
At this point, the bird looked too much like a standard sculpture, something someone could have carved out by hand; it didn’t quite have that modern flair that he wanted. It would also be really difficult, if not impossible, to make this design in real life at the scale that was intended. From here, Nico decided to use a technique called slicing to alter the model. Slicing is the process of taking a continuous 3d shape and breaking it down into flat stackable layers. This is helpful when someone intends on using a CNC mill, 3d printer, or laser cutter to make their project. Usually, someone uses software called a slicer to perform this function, but in this case, Nico wanted the project to be sliced in a very particular way. He wanted half of the bird to be made of panels that are stacked along a perpendicular axis to the other half of the bird. This created an asymmetry and movement in the design that wasn’t previously there.
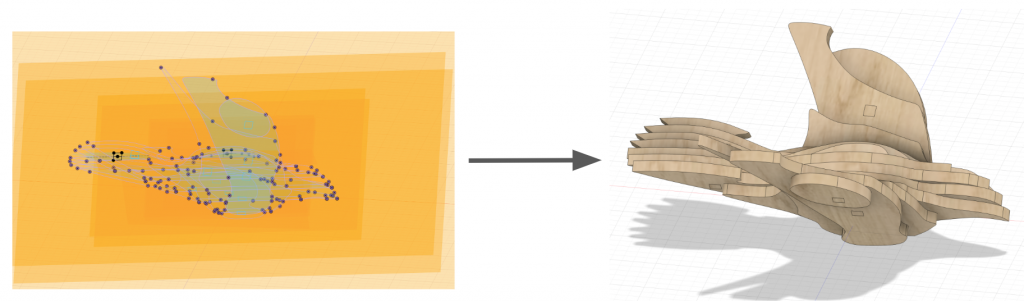
For the last touch, Nico created thinner panels on the outside of the bird that served a double purpose by adding subtle flourishes and hiding the ends of the pegs used to align the panels.
With the design finished, the stl files of each 2d profile were exported into Adobe Illustrator where they were scaled to the right size and aligned to fit the material Nico was cutting from. To test the functionality of the design, he started with a small prototype that was made from 1/4-inch pieces of wood cut from the laser cutter. He then used the Shopbot in the FabLab to make a larger version out of 1-inch foam boards. This way, he could dial in the proper settings for working with foam. Finally, he made the full-scale version out of 2.5-inch-thick foam boards on the Shopbot in the woodshop.
With all the pieces cut, he sanded down the edges, aligned and glued the panels together, painted it, and hung it up outside the fablab. Nico hopes that students will see it for years to come and get the same satisfied feeling when they look at it that he did when looking at student art during his time at Hawken.